Double-stage Vacuum Exhaust Ceramic Extruder
Three years ago, we introduced and optimized the improved German spiral ceramic membrane extruder technology to meet the urgent needs of Chinese water treatment industry users. In addition to using more cost-effective manufacturing parts, the extruder optimizes the replacement parts’ structure design to facilitate the daily maintenance of the extruder, optimizes the design of the vacuum exhaust structure of the extruder to avoid material agglomeration and drying which affects the product quality.
Our company pursues the extruder design on the basis of high cost-performance and lower energy consumption. At the same time, we insist on the pursuit of high stability and reliability of the extruder operation process, the intuitiveness and convenience of extruder control, and the convenience of daily maintenance. For this purpose, we have adopted supporting designs such as energy-saving frequency conversion control for the motor, human-machine interface, and modular core components. The barrel and screw of extruder core parts are made of special 17-4PH stainless steel, which has achieved ideal performance of high corrosion resistance and wear resistance, achieves the goal of longer extruder running time.
Configurations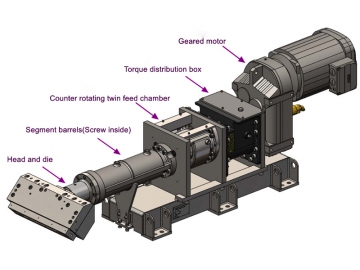
Feeding system | 120L volume 304 stainless steel hopper, and counter rotating feed screw provide a more positive feed and consistent flow of material |
Main motor and power | 75kw, high reliable variable frequency gear motor from China |
Screw diameter (mm) and manufacturing material | ¢1150 stainless steel |
Screw ratio (L/D) | 8 |
Screw speed (Wax.) | 50rpm |
Screw thrust (Max.) | 50Mpa |
Bearing torque (Max.) | 28650Nm |
Temperature control method | Constant temperature of soft water circulation inside both barrel and screw |
Temperature range | 10℃~100℃ |
Temperature control section for barrel | 5 sections |
Head pressure measurement and feedback | Equipped with American DYNISCO brand pressure sensor, with measuring range of 5000PSI |
Screw center height | 900mm |
Extrusion yield range | 500kg~800kg/hr, output varies with the ceramic membrane formula (such as alumina, titanium oxide, activated carbon, etc.) and the mold type |
Total installed capacity(kw) | 95 |
Electricity consumption in normal production | 85% |
Exterior dimensions | L2800mm×W900mm×H1300mm(Hopper height not included) |
Total weight(kg) | 4700 |
Power system | Motor/ reducer combination | A Chinese brand high-end & high-torque frequency conversion speed regulating is used, which has the characteristics of compact design and space saving, with large bearing torque, stable reliability and long service life. |
Transmission system | Torque distribution box | Radial bearing of torque distribution system adopts NSK brand, gear features high speed heavy load hard tooth surface, gear shaft material is 20CrNi2MOA with HRC58-62. |
Extrusion system | Feed device | 120L Volume stainless steel hopper, forced feeding system |
Barrel | External circulation constant temperature water control; there is a replaceable wear-resistant and corrosion-resistant liner made from 17-4PH H1150 stainless steel for internal barrel. | |
Screw | Screw is composed of wear-resistant and corrosion-resistant bimetallic thread elements, inside the core there is a soft water circulation temperature control system. | |
Temperature control system | Air-cooled chiller | Using air-cooled dual-system chillers, which are mainly equipped with European, America, Japanese compressors, Danfoss eco-saving components, as well as high-efficiency evaporators and condensers. The normal temperature water is cooled through the compressor mechanism of the chiller to the set temperature to force the control of the operating temperature of each barrel and screw section of the extruder. |
Electronic control system | Touch screen console plus Vertical control cabinet | Adopts a window-style 10-inch domestic high-end, stable and reliable touch screen, plus a PLC programmable logic controller to precisely control the system, and to realize PID tuning linkage of the main motor, screw speed and head pressure. The control operation function and main configuration of the system are as follows: 1. With the screw speed set on the touch screen as the standard, the PLC programmable logic controller controls the inverter to drive the 45kw main motor to realize the interlocking power control of the motor; 2. Control cabinet electrical devices, including contactors, air switches and solid-state relays, all adopt Chinese high-end brands, keeping the stability and reliability of the control system. Meanwhile, it has the functions of under-voltage protection and early warning, pressure protection and early warning, and realizes the protection and early warning function of 5℃~35℃ working temperature set on the control cabinet itself. |
Due to the extremely severe wear and corrosion conditions of the ceramic membrane extruder, the extruder provided by our company is accompanied by screw elements with 510mm length which on the most severe wear section. Secondly, in order to ensure the normal production needs of many users, our company also keeps a certain number of wear parts inventory for a long time to provide customers with after-sales service support.
Discussion on manufacturing materials for ceramic membrane extruder screwAlmost every user engaged in the extrusion of ceramic materials is concerned about the rapid failure of the screw due to the extreme friction wear and the extreme corrosion wear of the extruder, concerned about the short service life of the core components of the extruder. The following is the screw manufacturing material selection based on our experience for your reference.
- There are many ways to strengthen the screw surface, including bimetallic screw with a protective alloy layer on its working surface, the PM-HIP powder steel and the whole thread element is made of cemented carbide materials. For sample the ETC, a famous German ceramic extruder manufacturer, if ordered from low to high in cost configuration, there are 1.4112 quenched martensitic stainless steel type, powder metallurgy high temperature isostatic(PM-HIP) casting type and the all tungsten steel carbide type, etc., for their ceramic extruder screw;
Since the exhaust of ceramic materials in the extrusion process is very important, ceramic extruder generally needs to adopt a two-stage structure, the raw material is extruded from the upper extruder and then enters the bottom extruder after being vacuum exhausted. During the process of the material operation, the wear and corrosion of the material on the screw are different at the different positions, so the wear failure of the combined screw element at different positions is also different. In view of this difference, the best cost-effective method is to functionally configure threaded elements of different manufacturing materials for different positions of the screw.
For details, see the diagram as below.-
Some users have proposed whether it is possible to add ceramic coating on the surface of the screw to increase the service life, such as to increase alumina coating, as a company that has been engaged in the extruder industry for more than 30 years, especially in the research and development of materials for the core components of the extruder, we do not recommend the use of this coating method, the reason is:
A. In theory, whether it is aluminum oxide coating, nano-scale aluminum oxide coating, or aluminum oxide-titanium oxide coating, even carbide coating, etc., all belong to a ceramic coating. There are two kinds of coating forming process: Vapor deposition and liquid deposition. The fatal problem is that no matter which deposition process is used, the thickness of the coating is very limited. Generally speaking, the thickness of the vapor-deposited coating is only 0.006mm, while the thickness of the liquid-deposited coating can reach 0.02mm, but it is really very thin. Imagine that the material inside the ceramic extruder is entirely alumina (although there is a small amount of organic binder), and this large amount of alumina material against the 0.02mm thick coating on the screw surface under this shear friction, how this coating can withstand this friction? It can be concluded that no matter which kind of coating reinforcement the screw surface, the service life under this special working condition of the ceramic extruder must be very limited;
B. There are two major types of wear in all extruders under the working conditions. One type is the "shear wear" mentioned above when the screw edge pushes the raw material to move forward, and another type is "contact wear" between the surface of the screw ridge and the inner wall of the barrel because the screw cantilever is installed inside the barrel, which is also called as "matching wear" between the two metal materials. Theoretically, the matching wear coefficient between the same kind of metal materials is the largest, which is the easiest to be "rubbed off" each other. On a ceramic extruder running alumina materials, you can choose a tungsten carbide coating but can not be the alumina coating.
Below we exemplify the matching wear coefficients of materials between four types of metal, you can see the big difference:
-
The screw manufacturing cost of a ceramic extruder accounts for a very high proportion in the extruder quotation, that is if all threaded elements are made of tungsten steel, the calculated screw manufacturing cost will account for almost 40% of an extruder”s quoted price. For this reason, almost all famous extruder manufacturing companies in the world generally adopt the "functional configuration" method of screw element combination when facing extreme extruder wear conditions, such as German W&P company, German ETC company, etc, our company is no exception.
In terms of the functional configuration of the screw combination of the ceramic extruder, our company generally uses 1.4112 martensitic stainless steel for the screw elements of the upper extruder, and for the bottom-stage extruder, is configured with WR14 which is made by PM-HIP way on No. 1, No. 2 and No. 3 (see the threaded component configuration diagram above) positions, except these three positions, the other components are all made from 1.4112. Our company currently sells domestic and overseas markets according to this configuration, and has won unanimous praise from users in terms of cost performance.
WR14 threaded component manufacturing material is one kind of powder alloy tool steel imported from Europe with high chromium and vanadium content, so that WR14 alloy is with high wear resistance and corrosion resistance due to the existence of a large number of uniformly distributed hard carbides in the metal composition, at the same time, high density obtained by molding under a high temperature and a high pressure, so it has an excellent wear resistance and good toughness. And also the alloy has an excellent corrosion resistance due to the large amount of chromium inside the alloy composition.
The morphology, element composition, mechanical properties and anti-wear / anti-corrosion properties of WR14 powder steel are shown in the following table:
Our experience is that the targeted use of the above-mentioned functional configuration method of threaded elements of different manufacturing materials can obtain a very ideal cost-effective ceramic extruder.