Continuous Extrusion Line Components
Our range of copper and aluminum continuous rotary extrusion line refers to production lines for production various copper and aluminum products, including wire, busbar, strip, rod, bar, and more.
With the continuous extruding machine as the core unit, our continuous rotary extrusion lines are also available with auxiliary equipment such as straightening unit, cutting machine, oxidation prevention and cooling system, meter counter, take-up machine, payoff machine, among others. They are typically PLC controlled and are equipped with touch screen for main machine control as well. While offering failure alarming function, our range of continuous rotary extrusion equipment also supports automatic display of all technical parameters. These ensure easy operation, high stability and high efficiency.
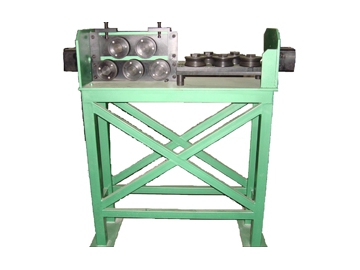
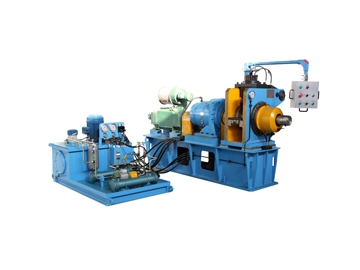
The continuous rotary extrusion machine, or simply continuous extrusion equipment, is mainly made up of the main drive system, auxiliary system and the control system.
(1) The main drive system adopts a DC motor to drive the spindle with the help of planetary gear reducer, thus generating the drive force to achieve continuous extrusion.
(2) The auxiliary system involves hydraulic, lubricating and cooling units. It is in charge of various ancillary operations as well as guaranteeing the operation of the main drive system.
(3) The control system makes use of DC speed governing technology to ensure rotation extrusion speed up to 11.5RPM.
The operation parameters, running status, and technical specifications can all be displayed and adjusted via the operation console and rocker arm control box.
The extrusion die is installed inside the die cavity, and the cavity is within a die shoe. The die shoe can be opened or closed for convenient changeover of spare parts and tools, driven by the hydraulic cylinder.
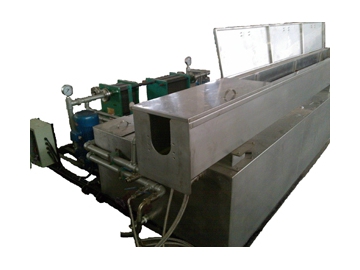
Our range of copper and aluminum continuous rotary extrusion line uses the self-circulated, forced water cooling method. A multistage pump is adopted for water supply. Equipped with a heat exchanger, the rotary extrusion line supports control the self-circulated cooling water temperature via the external cooling water.
The cooling system includes two parts: one for extrusion tools cooling, and the other for extruded products cooling.
(1) Due to the part for tools cooling, our continuous rotary extrusion equipment comes with extended service life.
(2) Protected by the oxidation protection tube, the copper and aluminum extrudate with high temperature is conveyed to the cooling tank for fast cooling to the normal temperature. Then, the extrudate is dried up.
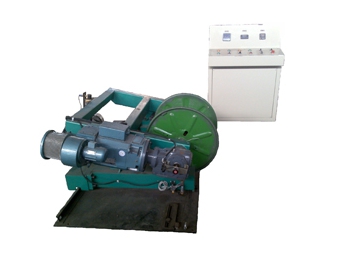
The ground rail style take-up machine functions to rewind copper or aluminum wires, busbars, and other extruded products under constant tension conditions. During rewinding process, the take-up reel will move left and right at a constant speed which is determined by the end product width, and the movement is controlled via a DC motor and an AC frequency converter.
The main motor of the take-up unit is available with a tachogenerator to control the array pitch. The take-up reel has diameter options from 630mm to 800mm.
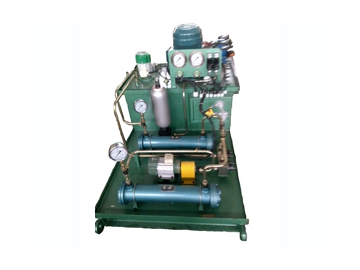
Hydraulic System
The hydraulic system of our continuous rotary extrusion line adopts highly reliable HUADE series hydraulic components. It is mainly composed of the pump motor group, pressure control unit, die shoe control unit, die shoe positioning unit, heat exchanger, oil filter, etc.
(1) The pump motor group serves to supply hydraulic oil.
(2) The pressure control unit is used for adjusting and controlling the working pressure.
(3) The die shoe control unit functions to move the die shoe out from or place into the extrusion head, thus making replacement of extrusion dies convenient.
(4) The die shoe positioning unit is employed to lock the position of the shoe.
(5) The temperature of the oil is controlled by the heat exchanger.
The lubricating system of our continuous rotary extrusion line includes two parts. One is called spindle lubrication system used for lubricating of the spindle bearing, and the other is the reducer lubrication. Both parts adopt the forced self-circulating lubrication method.
The lubrication oil is supplied by the gear pump, and the oil temperature can be controlled via the external circulating cooling water due to the employment of heat exchanger.
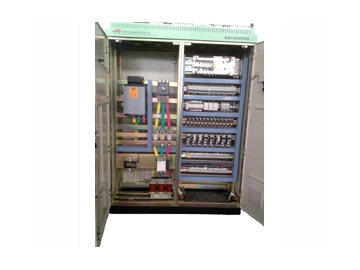
The electrical control system is an important part of the continuous rotary extrusion line. It includes the operation console, relay control cabinet and speed regulation cabinet. The low voltage electrical components all adopt the Schneider brand. The British Eurotherm speed governor and Japanese Mitsubishi PLC are chosen.
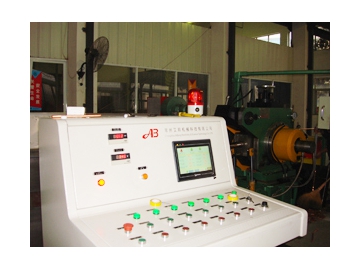
All production steps are controlled via the operation console which comes with the operation button, touch screen made in Taiwan, as well as the digital display meter for important process parameters. The touch screen supports functions such as equipment operation, parameter setting, operation status display, failure alarm, and technical curve display.