- width ≤ 0.25mm
- thickness ≤ 0.08mm
- no jagged edge
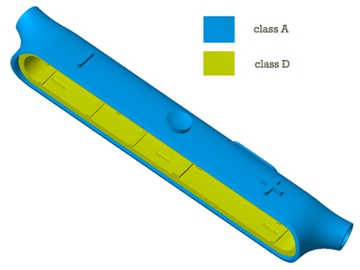
- light: 860~1600 LUX
- distance: 30~35cm
- starring time: 5 seconds
- eye inspection Angle: The line of sight is 90°from the inspection surface.
- D: the area covered by this diameter may be the same area of different shapes.
- N: number
- W: width
- L: length
Defective | Acceptable level of compression molding silicone rubber surface class X | |||
A | B | C | D | |
different color dot | D≤0.20mm N≤2 d istance>50mm | D≤0.30mm N≤2 distance>50mm | D≤0.40mm N≤2 distance>50mm | acceptable without functional failure |
similar color dot | D≤0.25mm N≤2 distance>50mm | D≤0.35mm N≤2 distance>50mm | D≤0.45mm N≤3 distance>50mm | acceptable without functional failure |
slight scratch | W≤0.08mm L≤1.5mm N≤1 | W≤0.08mm L≤2.5mm N≤1 | W≤0.15mm L≤8mm N≤2 | acceptable without functional failure |
scratch | N=0 | W≤0.08mm L≤1.5mm N≤1 | W≤0.15mm L≤5mm N≤1 | acceptable without functional failure |