Stationary Concrete Batching Plant with Bucket Elevator Feeding
Model: HZS25, HZS40, HZS50, HZS75
1. This particular concrete batching equipment comes with a bucket elevator feeding system and a concise modular structure. Both the installation and transportation processes are easy. There is only a limited installation space and investment needed.
2. This concrete mixing machine can produce various types of concrete, including plastic concrete, hard concrete and more, with a highly efficient production process. It can be widely used for the construction of projects such as mid-sized buildings, roads, bridges, airports, ports, railways and the concrete pre-batching plant.
3. As a professional construction equipment supplier, we have adopted the use of the JS series double horizontal shaft forced mixer, which features a perfect distribution, short mixing time, a long service life and is easy to maintain. Its mixing time is short and has a long consumable life as well as being easy to operate and maintain.
Model | |||||
Theoretical productivity (m3/h) | 25 | 40 | 50 | 75 | |
Mixer | Model | JS500 | JS750 | JS1000 | JS1500 |
Power (kW) | 18.5 | 30 | 2 ×18.5 | 2×30 | |
Discharge capacity (m3) | 0.5 | 0.75 | 1 | 1.5 | |
Max. aggregate diameter (grave/pebble, mm) | 60/80 | 60/80 | 60/80 | 60/80 | |
Aggregate bins | Volume (m3) | 4 | 4 | 8 | 8 |
Hoisting motor power (kW) | 5.5 | 7.5 | 18.5 | 22 | |
Scales capacity and accuracy | Aggregate (kg) | 1500 ±2% | 1500 ±2% | 2500 ±2% | 3000 ±2% |
Cement (kg) | 300 ±1% | 500 ±1% | 500 ±1% | 800 ±1% | |
Fly ash (kg) | - | - | 150 ±1% | 200 ±1% | |
Water (kg) | 150 ±1% | 200 ±1% | 200 ±1% | 300 ±1% | |
Additive (kg) | 20 ±1% | 20 ±1% | 20 ±1% | 30 ±1% | |
Discharging height (m) | 3.8 | 3.8 | 3.8 | 3.8 |
Note: All parameters are subject to modification.
Superior mixing performances
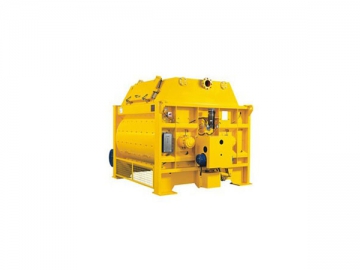
1. The concrete batching plant uses a forced type twin-shaft mixer which features a short mixing duration, rapid discharging process good material uniformity, and high productivity.
2. Our batch plant can achieve a desirable mixing performance for hard concrete, plastic concrete and other concrete formulas.
3. The mixer scale board and blade of the concrete batching plant are made of an anti-wear high chrome casting iron. Their angles are scientifically designed, which leads to a good mixing performance and long service life.
4. We use a unique design for the bearing support and sealing element. The two devices can be separated, and various bearing end sealing elements are adopted to make the sealing performance greatly enhanced.
5. The planetary reducer is purchased from Bonfiglioli, an internationally known company. The features include a small size, high efficiency, and are reliable.
6. An overweight design was adopted for the concrete batching plant, and the shock-absorption performance is excellent.
7. The discharge door is controlled by a hydraulic oil pump. There are three stopping points and a manual door opening device.
8. We use a centralized lubrication system powered by a 380V motor, which can inject the grease into the bearing end quickly.
Accurate and reliable electronic weighing system
1. The aggregate is measured using an electronic scale on the concrete batching plant. It can be measured separately or for the total weight.
2. Scale hoppers are used for the accurate weighing of cement, water, and additives. A microcomputer is adopted for the central control and is incredibly easy to operate.
3. The aggregate can be conveyed by using either the hopper elevator or belt conveyor.
High quality electrical components
We purchase the electronic components from internationally recognized brands or domestic companies, which ensures the reliability of our concrete mixing equipment during mass production.
1. The main transmission system of the concrete batching plant comes with a planetary gear from the Italian company Bonfiglioli. The reducers feature high transmission productivity rates and stable performances.
2. The Hymig or Airtac cylinders we use have a large overload capacity, a stable performance and a long life.
3. The selections of YSC or AIRTAC products have low failure rates and feature reliable performance capability.
4. Our air compressor comes from the American company Cheetah. There is a large gas displacement and the operation is steady.
5. The main electrical components of the concrete production equipment are from the French company Schneider, and the PLC is a Siemens product. These products are reliable and are highly efficient.
Comfortable Operating Room
The control room of the concrete batching plant is fully enclosed and air conditioned, thereby increasing the comfort of the operator.
Advanced and reliable electric control system
1. The whole concrete batching plant can be controlled automatically by the computer and the Siemens PLC or manually. The operation is very simple for operators.
2. A screen is designed to display real-time working conditions of different components and systems of the concrete plant. The data can be stored in the system and printed in a form for high management efficiency.
3. The user-friendly interface, can facilitate the on-site management and monitoring.
4. It has an automatic error compensation function, which can be done automatically.
5. Our concrete batching plant comes with two control mechanisms: an industrial touch screen and micro-computer. If the micro-computer fails to work, you can use the touch screen for system control, ensuring the production proceeds as normal.
Eco-friendly operation
All of the powdered materials are dispatched, measured, transferred and mixed in an enclosed environment, so the powder solution, shaking and noise are greatly reduced.