Automatic Rotary Injection Machine (One Mold for One Pair), EA110Q T/EA112Q T
This injection moulding machine is used to process different materials, like TPR, PVC and PUR and then produce products out of the materials, including single-colour foam or non-foam soles and slippers. What makes this injection press extraordinary is its ability to hold as many as 12 sets of molds, meaning that 12 pairs of shoes can be produced at a time.
Item | Unit | | |
Raw materials | TPR, PVC, PUR (blowing) | ||
Stations | 10 | 12 | |
Screw diameter | mm | 75 | |
Maximum injection volume | CC | 880 | |
Injection pressure | MPa | 70 | |
Clamping force | Tons | 60 | |
Yield | Pairs/hour | 100-200 | 120-240 |
Mould space | mm | 420*350*240 | |
Heating power | kW | 9 | |
Total power | kW | 36.5 | |
Dimensions | cm | 550×260×190 | 600×300×190 |
Machine weight | Tons | 7.5 | 8 |
Oil consumption | L | 700 | |
Other configurations | Water cooling system, servo motor and automatic skid system |
-
Water cooling system
-
Energy-saving hydraulic servo control system
-
Mould manipulator
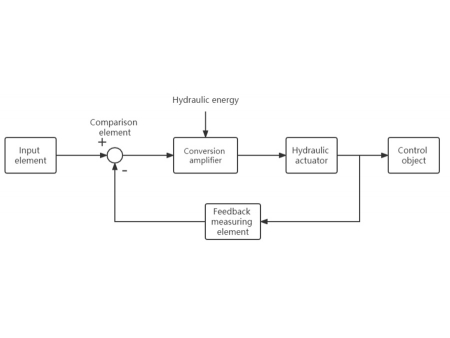
- Wide template design gives enough space for a dozen of molds;
- Efficient air blowing system is installed to improve the quality and reduce 30% weight of the goods to be made;
- Screw rod is made through special techniques, which ensures durability;
- Block cylinder is designed with special structure, providing heat insulation and leakage resistance performance;
-
PLC control system with industrial human-machine interface (HMI) is easy to use;
-
PLC system
-
PLC
-
HMI interface
-
-
Apart from these features, this injection moulding machine is equipped with several other parts to ensure the safety of operators and reduce costs. To be specific, the special designs include:
-
Safety sign
-
Safety signSafety door with photoelectric switch
-
Emergency stop button
-
Rotary table anti-lifting switch
-
-
Servo motor and automatic mould manipulator;
-
Energy-saving servo motor
-
-
Mold water cooling system is installed to speed up the cooling process, so as to improve production rate
-
Cooling tower is installed to lower the temperature of hydraulic oil and raw materials;
-
Crusher is installed to recycle used materials;
-
Vertical mixer blends materials with different colours and turn them into the same colour;
-
Horizontal mixer is installed to mix materials;
-
Air compressor is connected to the injection moulding machine to supply air;
-
Drying system is used to dehydrate air so as to avoid bubbles in finished products and make better foam soles;
Parts list | ||
Toolbox | / | 1pc |
Allen key | 1.5-10 | 9 sets |
Open-end wrench | 6-24 | 8 sets |
Phillips screwdriver (small) | / | 2pcs |
Phillips screwdriver (large) | / | 1pc |
Adjustable wrench | 250mm | 1pc |
Heating ring | Ø120*80 mm | 2pcs |
Heating ring | Ø70*50 mm | 1pc |
Heating rod | Ø15.8*100 mm | 2pcs |
Proximity switch | Ø 25*25mm | 1pc |
Proximity switch | Ø 12*12mm | 1pc |
Thermoelectric coupling | K type/5M | 2pcs |
Oil seal | / | 2pcs |
Plugging rod | / | 1pc |
Plugging bushing | / | 1pc |
Copper gasket | / | 1pc |
Injection nozzle | / | 1pc |
User manual | / | 1 |