Capability
Our design team has more than 10 years of experience in the industry and utilizes software like UG, PROE, and SOLIDWORKS to design tooling and dies for different mortise lock metal parts. Developing a new product begins with a description of ideal features that the lock will have. Once we have that, we will analyze the initial components and determine what will be needed to make a quality lock.
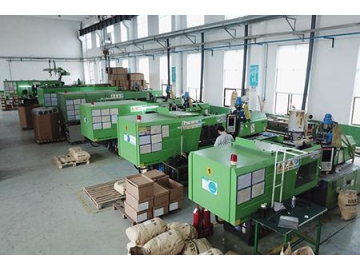
We have a fully equipped production facility to ensure a high level of productivity for bulk orders.
Injection molding- The lock's injection molding parts produced by our six injection molding machines, POM, Nylon, ABS and PC are the main materials used in our products. We have an output capacity of over 1 million injection molding parts per month.
- POM is a type of self-lubricating material with high intensity, some lock cases are produced using POM
- Some lock components use nylon because of its high intensity and its resiliency
- PC is known for its toughness and weathering resistance, making it an ideal material for the load bearing components of locks
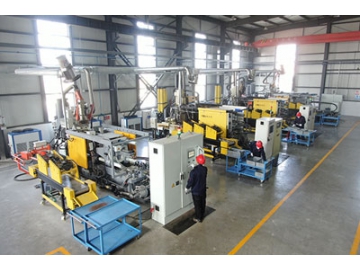
We have 2 sets of 288 ton cold chamber die-casting machines, 1 518 ton cold chamber die-casting machine, and 2 sets of 58 ton hot chamber die-casting machines. This equipment enables a high degree or production efficiency and reduces the overall production cycle. We choose die casting materials according to their tensile strength, resiliency, heat conduction, etc. Our die casting materials include ADC12, A380, A413, ADC1, ZAMAK3, ZAMAK5 and so on.
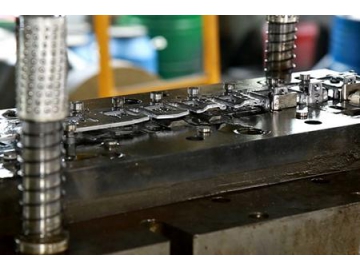
Our factory is equipped with 12 sets of high strength stamping equipment ranging from 63 tons to 1000 tons, which allow us to reach high-volume stamping production- 1 million stamping parts per month. Our stamping parts are commonly made from stainless steel and aluminum.
When parts are die-cast or injection molded, they typically have a rough surface or sharp edge. Therefore, it is essential to apply a machining process so that the lock parts can meet the precision requirements for assembly and operation.
In our machining workshop we possess a machining center, CNC lathe, multi-spindle tapping machine, driller, and other machining equipment. They allow us to complete various machining jobs in-house. Our skilled staff make the machining process more efficient.
To ensure the lock parts have a good appearance and perform properly, we always conduct surface treatments.
Nickel plating, chromate plating, spray painting, electrophoresis are commonly applied processes used for our die casting parts. They all give them a good locking surface and enhance the corrosion resistance of the parts.
Injection molded parts are typically treated with electroplating, spray painting, and vacuum plating. These treatments are designed to enhance the appearance of the products.
When it comes to finishing treatments for stamping parts, they optimize the anti-corrosion and appearance simultaneously. Additionally, various plating processes can be applied to stamping parts.
We operate a sophisticated ISO9001: 2015 certified quality management system. In this respect, our raw material outsourcing is strictly controlled and during production, inspections are carried out by experienced staff members. All products will undergo a salt fog test, acid resistance test, and paint adhesion test which meets Japanese standards.