Ceramics encompass a wide array of materials, including super-hard ceramics, high toughness ceramics, semi-conductive ceramics, magnetic ceramics, and transparent ceramics. With such a diverse array of types, they are used in an equally diverse array of applications, including machinery, chemicals, electronics, optics, aviation, military and more.
Main methods for ceramic material performance improvement: - grinding the ceramic material into particles as fine as possible
- controlling the ceramic particle size distribution to ensure performance won’t be affected by particles that are too wide
- increasing particle dispersion as much as possible
Because applications are significantly impacted by the grinding quality, ceramic materials must be fully ground before use. Our grinding mills meet all the challenges posed by a ceramic ultra-high hardness and ultra-high wear resistance, ensuring a top of the line final quality.
Shown here are the results from ultrafine grinding of different ceramic materials using our grinding machines. The particle sizes of these ceramic powders has been significantly reduced and distribution is exceptionally more uniform after grinding.
Grinding of silicon nitride (Si3N4) - Before grinding
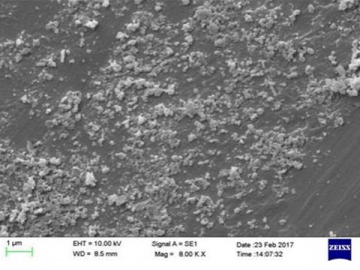
- After grinding
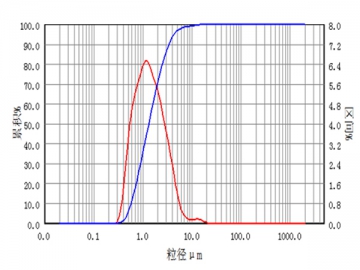
- Before grinding
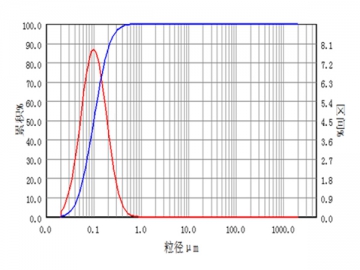
- After grinding
Characterized size | Feed | Products |
D50(μm) | 0.8 | 0.10 |
D90(μm) | 2.1 | 0.15 |
Grinding of hexagonal boron nitride (h-BN) 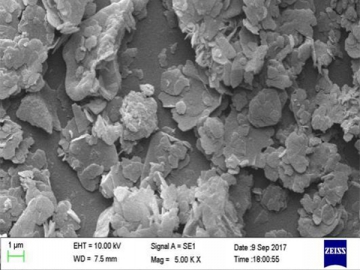
- Before grinding
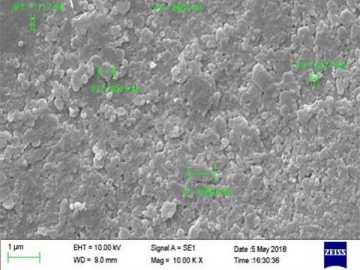
- After grinding
Characterized size | Feed | Products |
D50(μm) | 2.5 | 0.15 |
D90(μm) | 3.5 | 0.28 |
Grinding of silicon carbide (SiC) 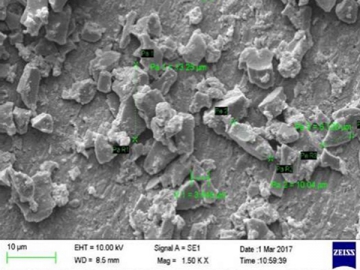
- Before grinding
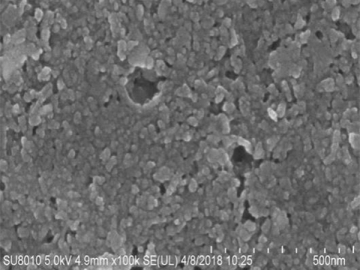
- After grinding
Characterized size | Feed | Products |
D50(μm) | 8.5 | 0.032 |
D90(μm) | 12 | 0.052 |
Grinding of boron carbide (B4C) 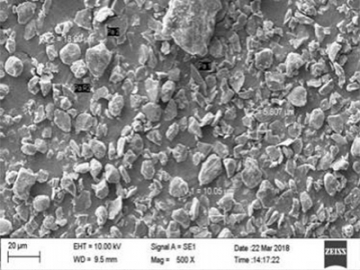
- Before grinding
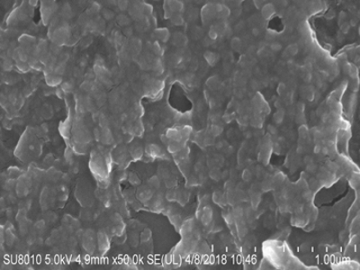
- After grinding
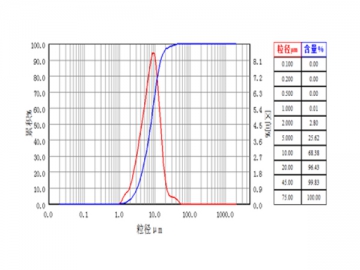
- Before grinding
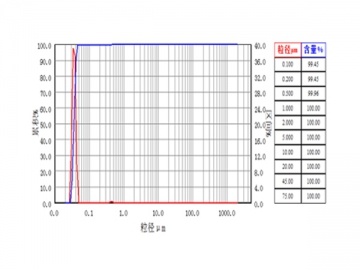
- After grinding
Grinding time | 0h | 3h | 12h |
D50(μm) | 7.7 | 0.48 | 0.035 |
D90(μm) | 14.8 | 0.66 | 0.053 |
Grinding of zirconia (ZrO2) 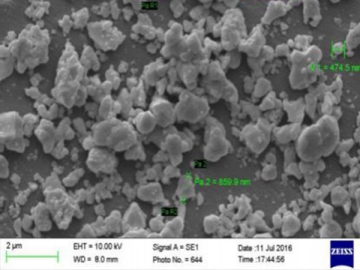
- Before grinding
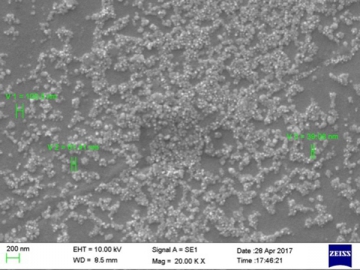
- After grinding
Characterized size | Feed | Products |
D50(μm) | 1.2 | 0.05 |
D90(μm) | 2.0 | 0.07 |
Grinding of zirconium silicate (ZrSiO4) 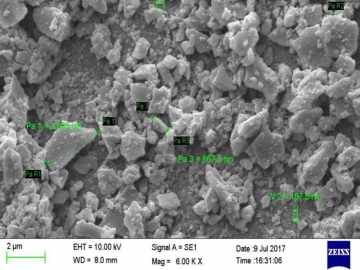
- Before grinding
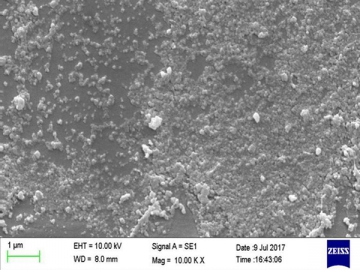
- After grinding
Characterized size | Feed | Products |
D50(μm) | 0.8 | 0.10 |
D90(μm) | 2.3 | 0.20 |
Grinding of strontium titanate (SrTiO3) 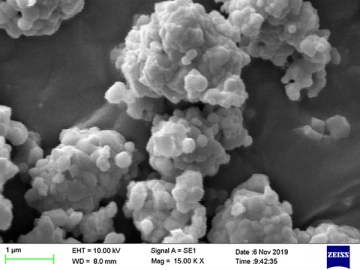
- Before grinding
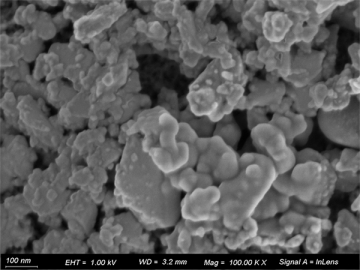
- After grinding
Characterized size | Feed | Products |
D50(μm) | 2.88 | 0.050 |
D90(μm) | 8.01 | 0.129 |
Grinding of barium carbonate (BaCO3) 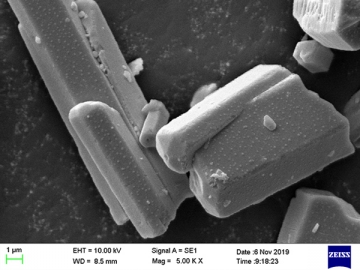
- Before grinding
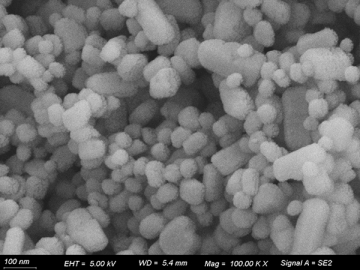
- After grinding
Characterized size | Feed | Products |
D50(μm) | 9.35 | 0.097 |
D90(μm) | 19.50 | 0.198 |
Grinding of α-aluminum (α-Al2O3) 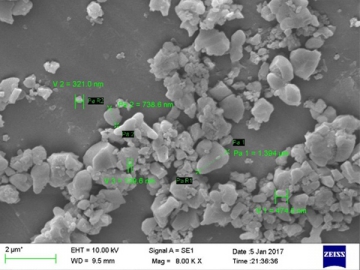
- Before grinding
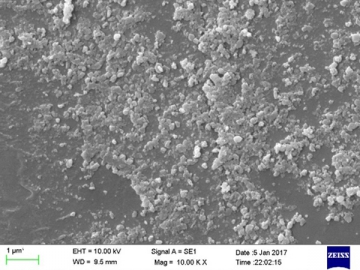
- After grinding
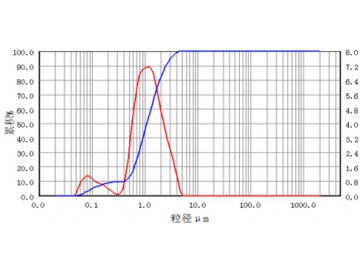
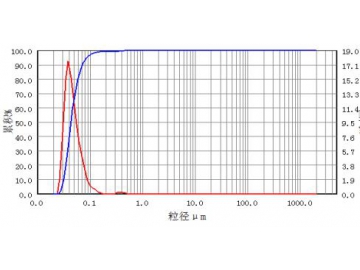
Characterized size | Feed | Products |
D50 | 1.2μm | 43nm |
D90 | 2.1μm | 71nm |