Metal powder is utilized not only as the primary raw material for powder metallurgy and 3D printing but is also used in coating utensils and jewelry.
Factors affecting metal powder properties include:1. Particle size Metal powder particle size and particle size distribution have a significant influence on finished product performance. The finer the powder, the better the bonding performance, and the finer the final product, the better the quality.
The metal powder particle size depends on the conditions under which the metal powder is prepared. As the following analysis displays, our grinding machines significantly reduce particle size up to nanometer levels.
2. Metal Powder Shape The strength, permeability, and uniformity of metal powder product properties are closely related to the metal powder particle shapes. The sphericity of metal powder usually needs to be over 60% when producing high permeability materials, which is effectively increased using our ball mills.
3. Metal Powder Specific Surface AreaThe specific metal powder particle surface area directly affects the metal powder’s sintering properties because most reaction starts on the metal particle surfaces.
Shown here are the results of an ultrafine material grinding, including aluminum, magnesium, iron, and aluminum-silicon alloys using our grinding machines. As evidenced by the ultrafine grinding, our grinders achieve a significantly reduced powder size, more uniform distribution, and a more standard metallic powder shape, thus effectively improving product performance.
Magnesium grinding - Before grinding
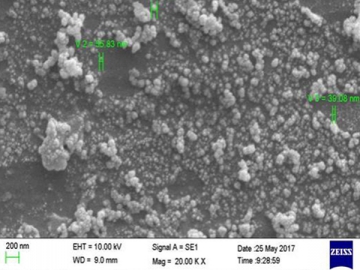
- After grinding
Characterized size | Feed | Products |
D50(μm) | 44.80 | 0.06 |
D90(μm) | 82.70 | 0.10 |
Grinding of aluminum-silicon alloys 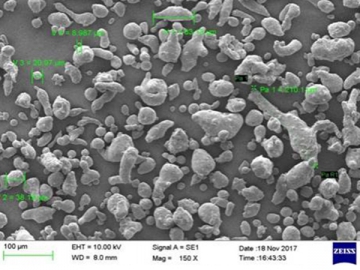
- Before grinding
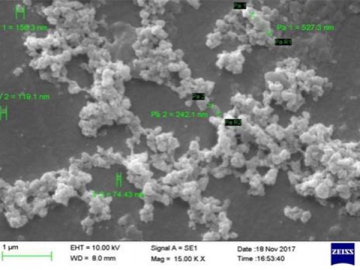
- After grinding
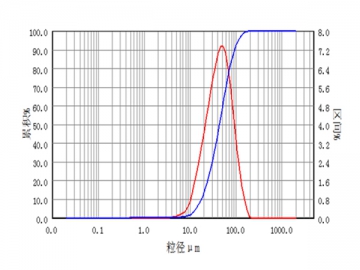
- Before grinding
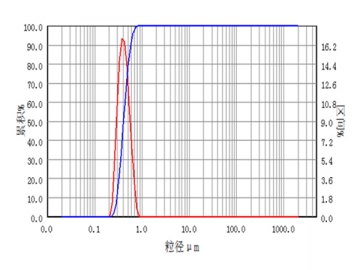
- After grinding
Characterized size | Feed | Products |
D50(μm) | 43.00 | 0.35 |
D90(μm) | 93.00 | 0.52 |
Grinding of zinc oxide (ZnO) 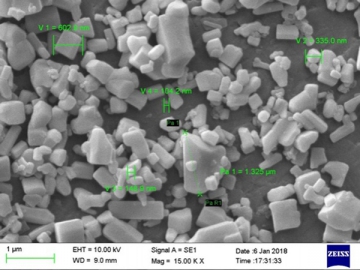
- Before grinding
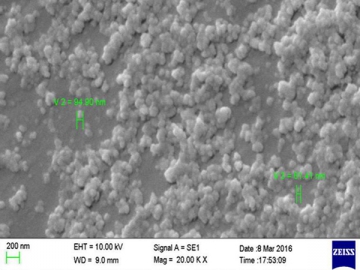
- After grinding
Characterized size | Feed | Products |
D50(μm) | 0.44 | 0.07 |
D90(μm) | 1.20 | 0.10 |
Grinding of tungsten trioxide (WO3) 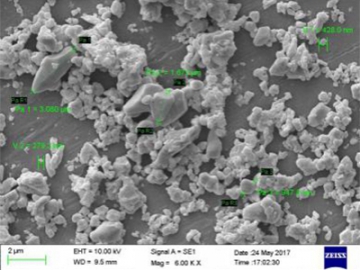
- Before grinding
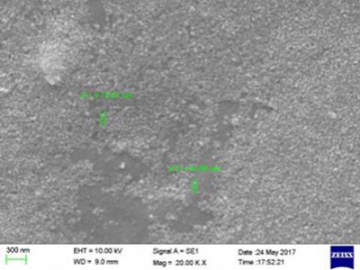
- After grinding
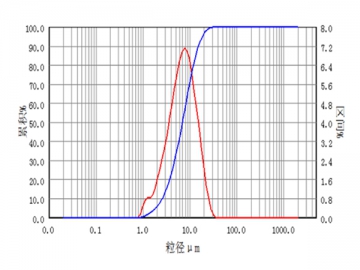
- Before grinding
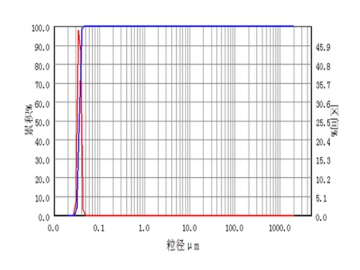
- After grinding
Characterized size | Feed | Products |
D50(μm) | 6.90 | 0.04 |
D90(μm) | 15.30 | 0.07 |
Grinding of manganese dioxide (MnO2) 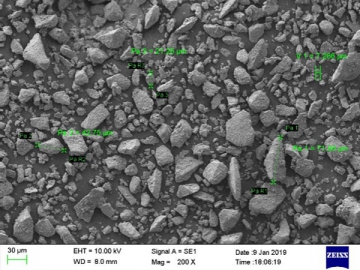
- Before grinding
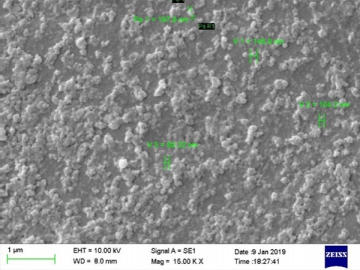
- After grinding
Characterized size | Feed | Products |
D50(μm) | 21.25 | 0.08 |
D90(μm) | 42.75 | 0.14 |
Grinding of cerium dioxide (CeO2) 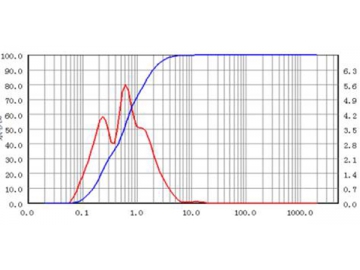
- Before grinding
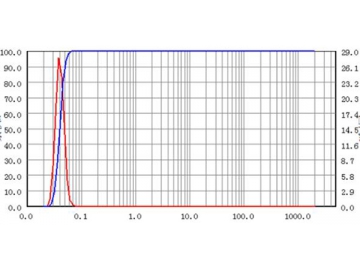
- After grinding
Grinding time | 0h | 1h |
D50(μm) | 1.6 | 0.04 |
D90(μm) | 2.1 | 0.03 |
Grinding of yttrium oxide (Y2O3) 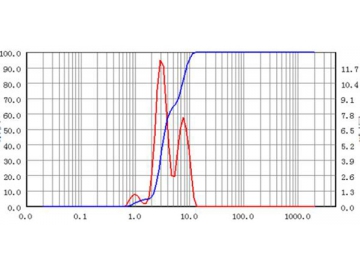
- Before grinding
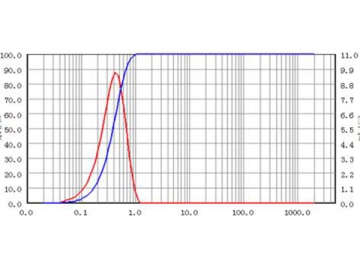
- After grinding
Grinding time | 0h | 1h |
D50(μm) | 3.6 | 0.38 |
D90(μm) | 8.8 | 0.67 |
Grinding of titanium oxide (TiO2)
- Before grinding
- After grinding
Grinding time | 0h | 6h | 8h |
D50(μm) | 2.6 | 0.065 | 0.05 |
D90(μm) | 7.3 | 0.100 | 0.08 |