Precision Fluorine plastic tube extrusion line
Fluorine Plastic Tube Extrusion Line / Plastic Tube Extrusion Line / Precision Plastic Tube Extrusion Line
Fluorine plastic is a paraffin polymer in which all or part of the hydrogen is replaced by fluorine. Fluorine plastic tube types include polytetrafluoroethylene (PTFE) (not extrusion processing), total fluoride (ethylene propylene) (FEP) copolymer, poly full fluorine alloy (PFA) resin, poly trifluorochloroethylene (PCTFF), ethylene fluoride, a vinyl chloride copolymer (ECTFE), ethylene suites fluoride (ETFE) copolymer, poly (vinylidene fluoride) (PVDF) and polyvinyl fluoride (PVF).
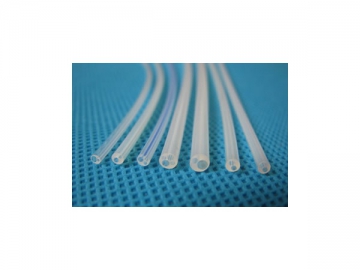
Compared to general plastics and engineering plastic, fluorine plastics have more outstanding physical properties, including a wide temperature range, a unique hardness, excellent wear resistance, and a high resistance to chemicals and heat. For application requirements, fluorine is widely used in medical, automotive and communication industries.
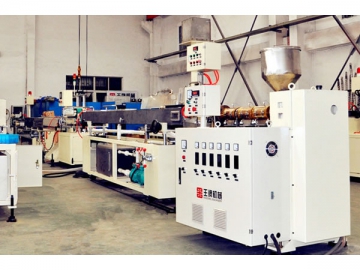
Kingswel Machinery Baochong Extrusion Company has several years of experience in the research, development and debugging of various plastic tube extrusion lines, particularly for medical fluorine plastic conduits and multilayer, composite automobile tubing products in order to provide a stable and reliable set of extrusion equipment, debugging process guidance and a full range of turnkey service.
Fluorine Plastic Tube Extrusion Line Features
The barrel and screw on the extruder utilize GH113 steel material, and feature an excellent corrosion and high temperature resistance, meeting the processing requirements for fluorine plastic extrusion plasticizing.
The heating component in the barrel is made of copper or cast steel, meeting stable production requirements at an extremely high processing temperature of 500°C.
The die uses an advanced CNC processing technology and an electrochemical machining method for precision processing and meeting a diameter range of ≤1.0mm for ideal tube forming.
The vacuum control is more precise, and achieves an accuracy control of -0.1Kpa levels.
Various fluorine plastics have a different processing temperature, melting viscosity and liquid flow rate, meaning the corresponding calibration has to have just as much variety, including a vacuum dry calibration, vacuum immersion bath calibration, internal pressure calibration and other methods.