Closed Cycle Spray Dryer
General description for BGZ Series Closed Cycle Spray Dryer:
The Closed cycle spray drying system is mainly used for solvent with ethyl alcohol and other combustible and explosive substances in the slurry or the products subject to oxidation when exposed to air. This machine, that can deliver products of good uniformity and produce spherical materials, is especially applicable to medical intermediates and high-precision ceramics, such as tungsten carbide, silicon nitride and nano-ceramics, pharmaceutical intermediates.
Operation Features:
1.It can prevent the products from oxidizing and improve the quality of products.
2.It is easy to realize the dust free and aseptic operation.
3.It can recover the solvent in the material liquid.
4.It can improve the preservation of fragrant composition.
5.It can dry the flammable liquid material or conduct cooling granulation.
6.It can dry the material with strong heat sensitivity.
7.It can realize the less public hazards or no public hazards.
8.It can leave out the deodorization device.
9.It can realize the low temperature drying below 100℃.
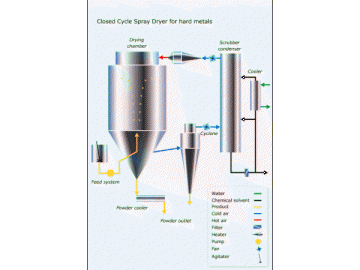
Operating Principle:
The closed circulation spray drying system is operated in a closed environment with inert gas (generally N2) as the drying medium. It is suitable for drying of materials containing organic solvent or poison gas or subject to oxidation in the process. This system uses inert gas as the circulating gas that passes the wetting and dewetting processes for protection of the drying material, and the medium can be reused; nitrogen enters the drying tower through the heater, and liquid material is delivered by the screw pump to the centrifugal nozzle, atomized by the high-speed circulating atomizer into powders and discharged from the bottom of tower; under the action of negative pressure of the fan, the evaporated organic solvent gas is dedusted by the cyclone separator and spray tower, then the saturated solvent gas is condensed into liquid and discharged from the condenser; the non-condensed gas medium is reused as dry carrier in the system after continuous heating. However, common centrifugal spray dyer realizes the purpose of moisture removal by continuous air blowing and venting, which is a distinctive difference between the explosion-proof closed centrifugal spray dryer and common centrifugal spray dryer. With inert gas as the drying medium, the drying system is internally operated under positive pressure; therefore, certain positive pressure should be maintained. When internal pressure decreases, the pressure transmitter is activated for automatic control of feed rate and ensuring pressure balance of the system.
Process Description:
The YGGZ closed circuit pilot spray dryer, is specially designed to carry out a rapid low temperature conversion of liquid products to powders in experimental scale or for small scale production. The drying process is carried out in an inert gas (Nitrogen). Applications are found throughout the chemical, pharmaceutical and food processing industries where protection against oxidation, fires or explosions is necessary.
The liquid product is fed to the atomizer system by a pump from a stirred holding vessel to the atomizer.
The liquid feed is atomized by a two-fluid nozzle co-current or counter-current to the gas-flow or, alternatively, by an ex-proof centrifugal atomizer.
The drying gas is heated by means of electricity, filtered in a HEPA filter, and enters the chamber via a specially designed gas distributor.
The drying chamber has a conical bottom with a 50o cone angle. The chamber is provided with door, light and sight glass.
The drying gas leaves the drying chamber together with the powder and is transferred to a cyclone where the powder is separated. The gas is subsequently cleaned in a bag filter, and then taken through a HEPA filter.
The cleaned gas is led to a tubular surface condenser where the water or solvent is condensed and separated. The dry gas is recycled to the gas heater.
The plant is delivered with an instrument panel including necessary control and instrumentation.
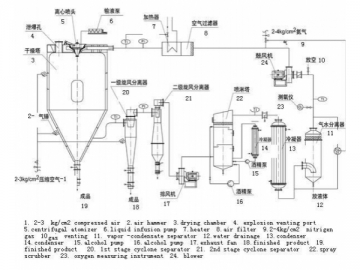
Scope of Application:
Non-oxide ceramics (AeN, Si3N4 etc.), hard alloy, high-performance battery materials;
condiments, health-care products; medicine, vitamin and organic chemicals; synthetic resin, paraffin; anti-explosion hazardous products with alcohol, soybean protein powder, bean pulp-EGBE, guanidine nitrate, sodium cyanate, diacetone, acetonitrile and chemical and intermediates etc.
We will provide the reasonable parameters reference according to the specific URS.
Attentions before Order:
Liquid name and property:solid contents(or water contents),viscosity,surface tension and PH value;
Dry powder density residual water contents allowed,particle size,and maximum temperature allowed.
Output: shift time daily;
Energy that can be available at user’s site: steam pressure, electricity properly,fuel of coal,oil and natural gas;
Control requirement: whether or not the inlet and outlet temperatures should be controlled. Whether the whole control system should be fully automatic or semi-automatic;
Powder collection requirement: whether it's necessary to use cloth bag filter and the requirement of the environment of the exhausted gas.
Other special requirements.